Gavin Harper, University of Birmingham and Allan Walton, University of Birmingham
It wasn’t so long ago that the UK prime minister, Boris Johnson, said wind turbines “couldn’t pull the skin off a rice pudding”. He now seems to have undergone something of a Damascene conversion, promising to boost the government’s target for offshore wind deployment to 40 gigawatts (GW) by 2030. Enough, he claims, to power every home in the country.
Offshore wind energy is cheaper than gas power stations or nuclear power, so economically this is a policy no-brainer. The Committee on Climate Change has stated that the UK’s offshore wind capacity should be 75GW by 2050 to achieve net-zero emissions, while others imagine even more ambitious scenarios, so redoubling commitment to offshore wind is welcome.
The government estimates the policy will support up to 60,000 jobs directly and indirectly by 2030. How many of these turbines will be made in the UK is unclear, but “government sources” are alleged to have promised that 60% will originate in Britain. An independent assessment concluded the government would need to commit almost £50 billion (USD$64.5 billion) to pull this off – substantially more than the £160 million currently pledged to upgrade the UK’s ports and factories.
But there’s another, perhaps bigger problem, that few seem to have noticed. The largest offshore wind turbine, the Siemens Gamesa 14MW has blades 108 metres long. Repairing gearboxes high up and in the middle of the sea is tricky, so these modern turbines are designed with incredibly powerful permanent magnets that can produce electricity without a gearbox.
These tremendous turbines require enormous quantities of magnetic material – so called “rare-earth magnets”. Even a wind turbine rated at 5MW requires around three tonnes of magnets, of which one tonne is rare earth metal, such as neodymium and dysprosium.
The UK has little to no native deposits of these metals, so where will this material come from?
‘The ace in China’s hand’
Boris Johnson declared “as Saudi Arabia is to oil, the UK is to wind”. This may be true, but exploiting this advantage will require turbine generators stocked with rare earth metals. “Rare” is a bit of a misnomer though. The material isn’t all that scarce and the world isn’t at risk of running out. It does occur in relatively low concentrations where it is found though. This makes it challenging to refine enough of it and China presently controls most of the world’s supply chain.
In an echo of Johnson’s verbal flourish, Chinese leader Deng Xiaoping once remarked on a tour of a rare earth production facility in 1987 that “the Middle East has oil, China has rare earths.” More recently, Chinese state media referred to rare earth metals as “the ace in China’s hand”. It’s clear China’s leaders haven’t forgotten their significant advantages in the global race to clean energy.
While the EU recently published its strategy for obtaining these critical materials, Brexit means that the UK must consider its own position independently. So what might that look like?
What’s the solution?
The price and supply of rare earth metals can be volatile, so developing a broader base for their supply is important. Exploring alternative sources of metals such as neodymium is one option, but the processes for mining these rare earth materials can cause a lot of pollution.
The UK might be overlooking an indigenous supply of rare earth magnetic material in many of the waste electronics it discards. Motors, pumps and electronic goods such as speakers and hard disk drives all contain them. All that is needed to exploit this is a capable recycling industry, and that’s something the University of Birmingham is looking into.
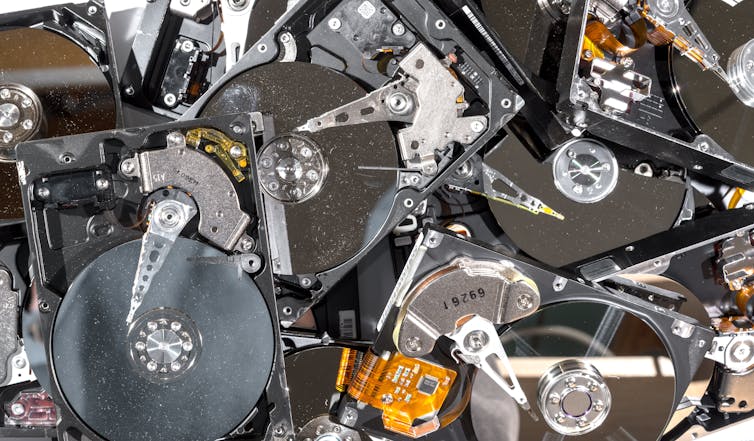
Diversifying the raw material supply and recycling used magnets are not mutually exclusive. There could be a lot of overlap between the technologies and processes used for treating mined and recycled material. The UK should develop a coordinated approach to both, and there are promising signs the government is considering the challenges involved.
The UK’s demand for rare earth metals will only increase, so robust policy for sourcing them and ensuring a cost-effective supply to UK industry will be essential.
In the future, we’ll also need to think about how to recycle the material in these turbines at the end of their 20 to 25-year lifetime. As global demand for metals such as neodymium grows, this offshore reserve of critical materials may prove to be a shrewd investment.
Gavin Harper, Research Fellow, Birmingham Centre for Strategic Elements & Critical Materials, University of Birmingham and Allan Walton, Professor of Critical and Magnetic Materials, University of Birmingham
This article is republished from The Conversation under a Creative Commons license. Read the original article.